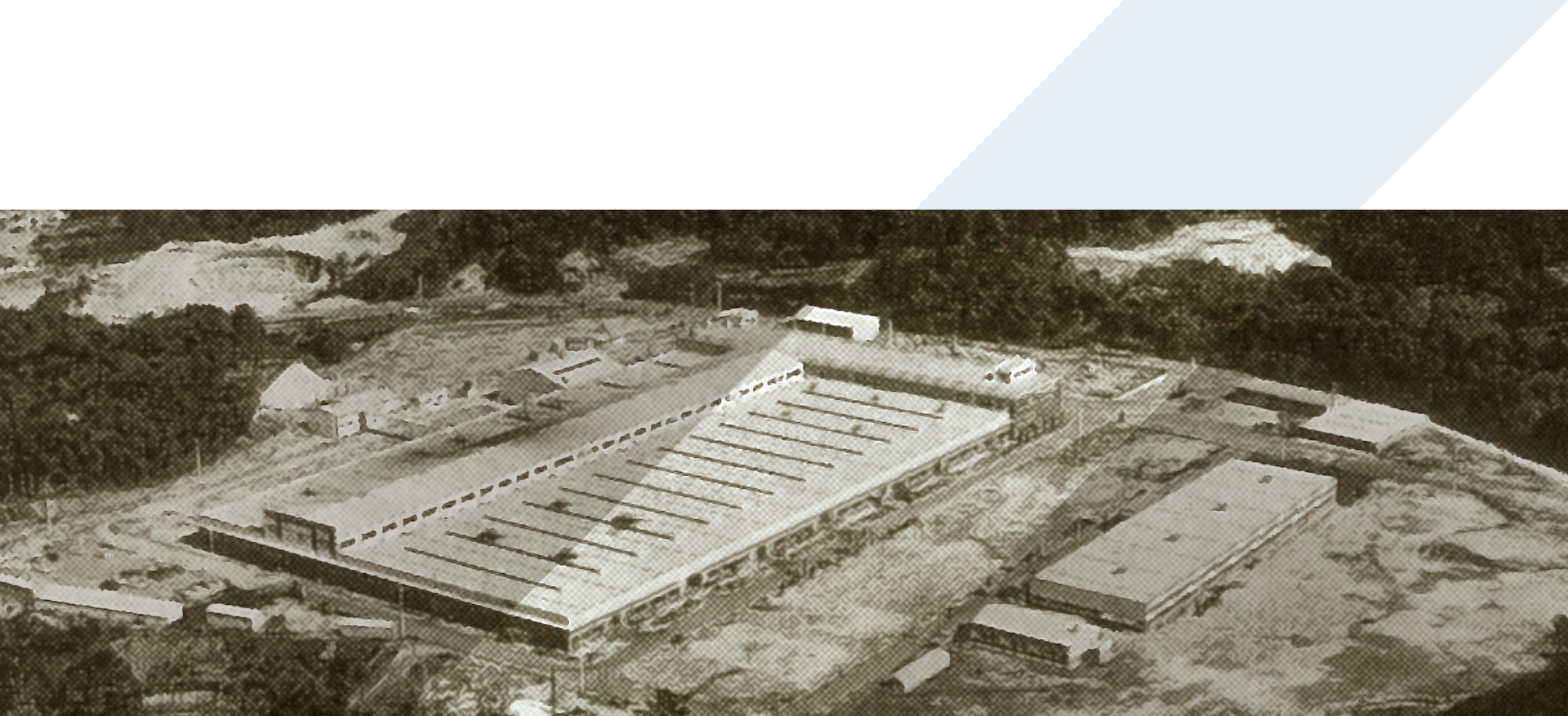
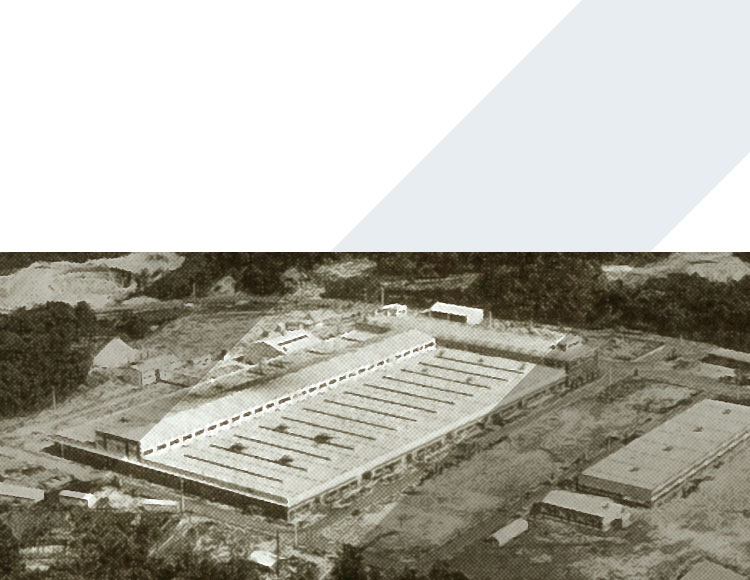
historyヒストリー
It's HAMANA's DNA
浜名部品工業
開発 × 挑戦 ヒストリー
数えきれない開発と挑戦を繰り返して歩んできた、浜名部品工業。
そんな当社の歴史を決定づけた、年表には描ききれない出来事を紹介します。
1960年代
|
1970年
20社が結集! 浜名部品工業の前身
富士機工株式会社に製品を納入していた湖西市内の約20社が集まり、「富士機工協力協同組合」を結成したのが浜名部品工業のルーツです。切削・ブレス・溶接・めっき・塗装など、それぞれ得意分野を持った専門家集団がひとつにまとまることでお互いの強みを引き出し合うという、先進的な取り組みでした。現在の浜名部品工業の強みである一貫体制は、ここから始まっているのです。
独立したメーカーとして歩み始める
結成後、数年をかけて各社の合併や離脱を経て7社になった「富士機工協力協同組合」は、「浜名部品工業協同組合」に改称して、組織としての独自性を高めていきます。このころには各社の工場が集結し、現在の浜名部品工業の敷地に匹敵する一大工場群が誕生していました。
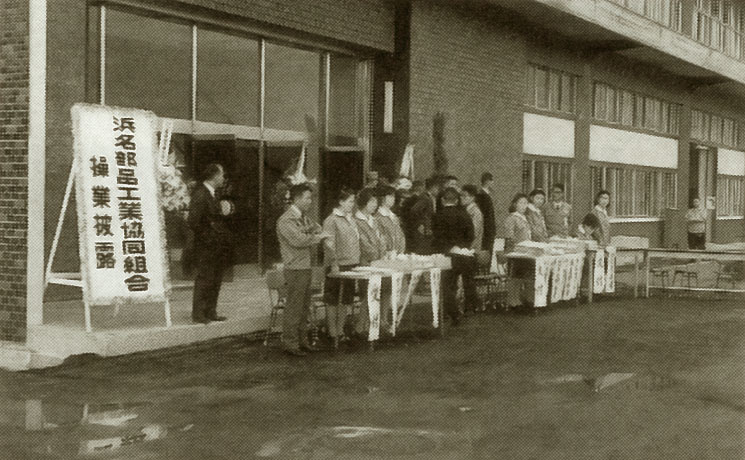
1970年
8月
「浜名部品工業株式会社」設立へ
1970年8月、「浜名部品工業協同組合」の各社が合併して、従業員数633名という湖西市有数の企業、「浜名部品工業株式会社」が誕生しました。当時の主力品目は、主に日産自動車(株)向けのクランクプーリーやステアリングシャフト、トルコンカバーなど。このころからシフトレパー用の部品も生産していましたが、当時はまだ組立のみの請負でした。
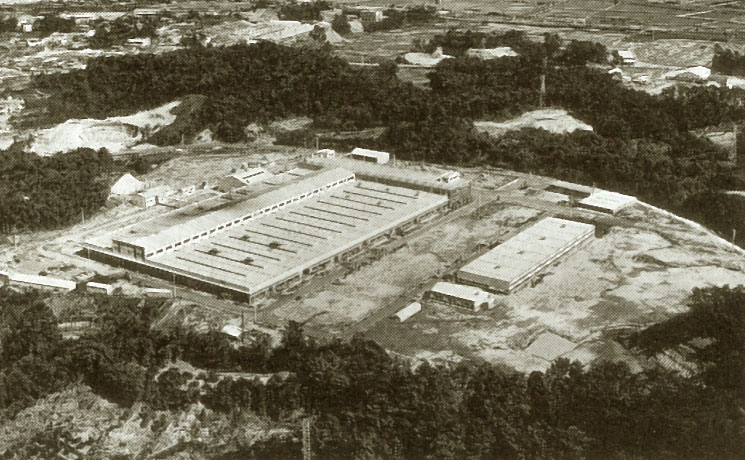
1975年
4月
冷間鍛造工法の導入と、「承認図形式」の始まり
当時、熱間鍛造工法で生産していたキャリー系のプロペラシャフトの生産効率を高めるために、その構成部品のひとつである「ヨーク」の工法転換を鈴木自動車(現スズキ)に提案したのが、当社における冷間鍛造工法の始まりです。これまでとは全く違う工法のため、当時の技術陣はGW返上でプレゼン・交渉に臨んだといいます。
また冷間鍛造工法の提案では、もうひとつの大きな成果がありました。「承認図形式」と呼ばれる生産プロセスの始まりです。これまでの部品生産は、「設計は自動車メーカー、生産は部品メーカー」という役割分担が当たり前でした。それに対して、浜名部品工業が設計し、強度検討まで行った図面を自動車メーカー側が承認するという、開発・提案型の生産方式を確立したのです。
この「冷間鍛造工法」と「開発・提案型のものづくり」は、現代まで続く浜名部品工業の強みになっていきます。
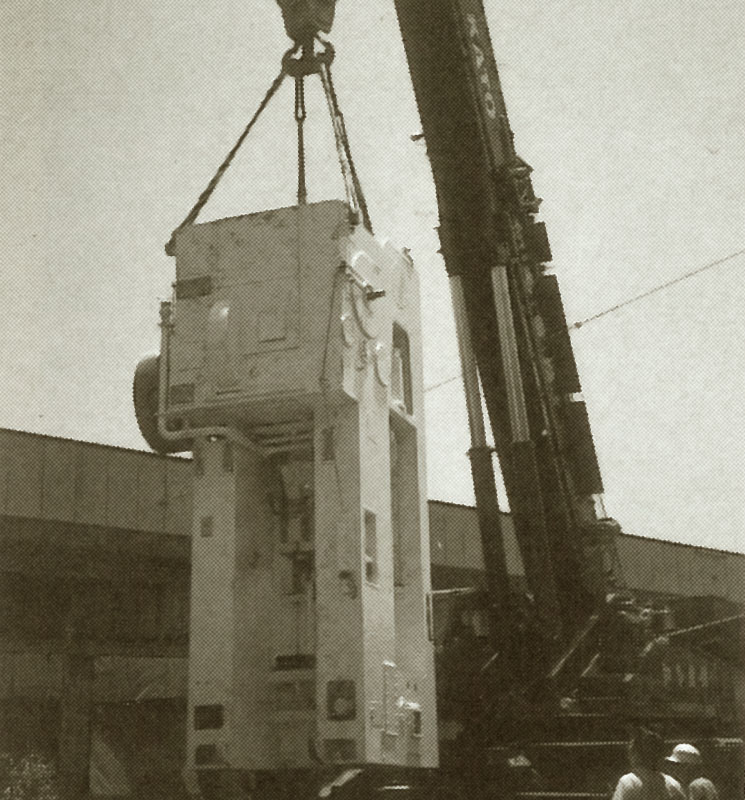
COLUMN
「町の発明家」と称賛された、冷間鍛造技術への挑戦
当社を代表する強みのひとつ、冷間鍛造技術。実は、ひとりの役員(後に社長)の飽くなき挑戦が実を結んだものでした。
「浜名部品工業株式会社」の誕生以前から冷間鍛造に興味を持っていたこの役員は、合併によってさまざまな技術が結集したことで研究を本格化。社内から数人の技術者を募って開発部を立ち上げ、約5年の歳月をかけて冷間鍛造技術を実用化したのです。その最初の製品こそが、上で触れたキャリー用プロペラシャフトのヨークでした。その研究姿勢と情熱は、鈴木自動車の設計者から「町の発明家」と称賛されたそうです。
1982年
ラインごと借りて、新製品に挑戦
1982年に生産が始まった「クランクシャフトとカムシャフト」は、当社の歴史の中でもユニークな存在。なぜなら、当時の浜名部品工業にはこれらの製品を作るための人員と場所はありましたが、肝心の生産設備がなかったのです。そこで、お客様である鈴木自動車工業から生産ラインを丸々借りるという思い切った発想で生産を受け入れ。実際の生産を行いながら、自社技術や設備の拡充を進めていきました。
1983年
特機製品の組立を開始
1980年代は、好景気に支えられて日本のものづくりの多様化が進みました。当社でも、鈴木自動車の特機製品の組立を受入。浜名部品工業の工場内にスズキ社の組立工場と完成品倉庫があり、完成品が浜名部品工業の正門を通って出荷されるという、変則的な生産を行っていました。これが、後に当社がセニアカーやモーターチェアの販売を行うルーツとなります。
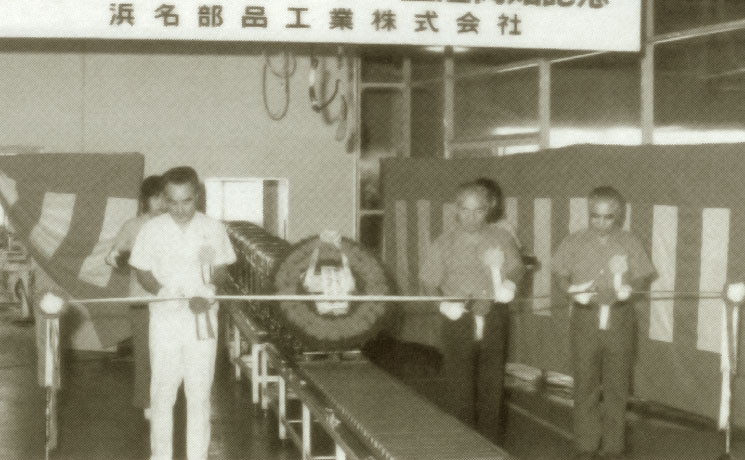
1990年
|
2000年
人海戦術からオートメーションへ
1990年初頭、需要の拡大に対応するために三ケ日工場を造設。この時代は自動化技術がまだ発展途上だったので、生産の増加に対して生産設備の数を増やすことしか対応できなかったともいえます。それを裏付けるように、2000年代にかけてオートメーション化が進むと、今度は再び本社工場に生産を集約するようになっていきます。
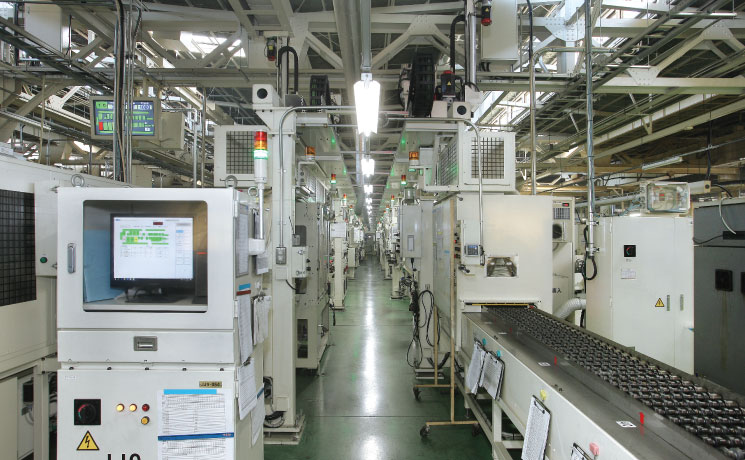
2003年~
浜名部品工業発信で、新しい分野へ
2000年代に入って一層注力するようになったのが、当社の強みを生かしてお客様に新しい価値を届ける「VE・VA提案」です。たとえば、従来は熱間鍛造で造られていた部品を冷間鍛造で作ることで省コスト・エコロジー化を達成したり、表面処理や組立などプロセスごとに数社が関わって造られていた製品を一貫生産したりと、お客様、浜名部品工業双方に利益のある提案を行い、これまでにない分野を開拓していきました。最初は一筋縄ではいきませんでしたが、現在ではベアリングのアウターレースの生産や精密部品の表面処理など、従来にはなかった製品分野にラインナップを拡げています。
2008年~
新たな“一貫体制”への挑戦
2008年に生産を開始したATセレクター。浜名部品工業の、新たな“一貫体制”への挑戦です。当初は社内に樹脂製品の製造技術がなかったため、部品を社外で製造してもらって組立てのみを担当していました。しかし2011年からは樹脂成形機を導入し、部品製造を徐々に内製化。現在では金属加工技術と樹脂成形技術を組み合わせ、高品質・低コストを両立した魅力ある製品を生み出しています。
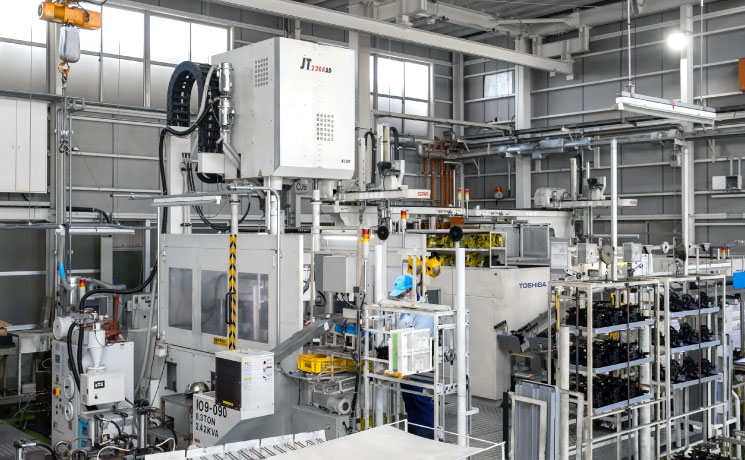
2023年~
二輪・四輪ほとんどのスズキ車に、浜名のカムシャフト
1982年、借り物の生産ラインで製造を始めたカムシャフト。現在では二輪車、四輪車に向けてさまざまなカムシャフトを生産していますが、特にスズキ車における浜名部品工業のシェア拡大は特筆もの。2023年現在では、一部を除いてほとんどの二輪・四輪のスズキ車に浜名部品工業製のカムシャフトが使われています。

開発×挑戦の歴史は続く
時には時代に応じて、時には時代に先んじて、さまざまな基盤技術や生産技術を開発してきた浜名部品工業。
カーボンニュートラル社会の実現に向けて待ったなしの挑戦が続く今、環境負荷を低減しながら高品位な製品が製造できる冷間鍛造技術や、製品の軽量化に役立つ樹脂技術など、当社の保有技術はいまだ大きな可能性を秘めています。
浜名部品工業はこれからも冷間鍛造技術を軸に据えつつ、周辺技術の獲得などの「開発と挑戦」をさらに進めて、幅広い産業分野に貢献していきます。